For screw fasteners production, surface treatment is a process with the inevitable, many vendors in inquiring about the screw fasteners, way of surface treatment, the standard network according to the summarized information about the surface of the screw fasteners common processing ways there are eight kinds of forms, such as: black (blue), phosphating, hot dip zinc, dacromet, electric galvanized, chrome plating, nickel and zinc impregnation. The fastener screw surface treatment is through a certain method to form a covering layer on the surface of the workpiece, its purpose is to make the surface of the product beautiful, anti-corrosion effect.
Eight surface treatment methods for fastener screws:
1, Black (blue)
The fasteners to be treated with black were placed in the solution tank (145±5℃) of sodium hydroxide (NaOH) and sodium nitrite (NaNO2) oxidant heating and oxidation, the surface of the metal fasteners generated a layer of magnetic Fe3O4 (Fe3O4) film, thickness is generally 0.6 — 0.8μm black or blue black. Both HG/20613-2009 and HG/T20634-2009 standards for fasteners used in pressure vessels require blue processing.
2, Phosphating
Phosphating is a process of forming phosphate chemical conversion film by chemical and electrochemical reaction. The phosphate conversion film is called phosphating film. The purpose of phosphating is to provide protection for the base metal and prevent the metal from being corroded to a certain extent. Used as a primer before painting to improve the adhesion and corrosion resistance of the paint film; It can be used for friction reduction and lubrication in metal cold working process. The standard for large diameter double – headed studs for pressure vessels requires phosphating.
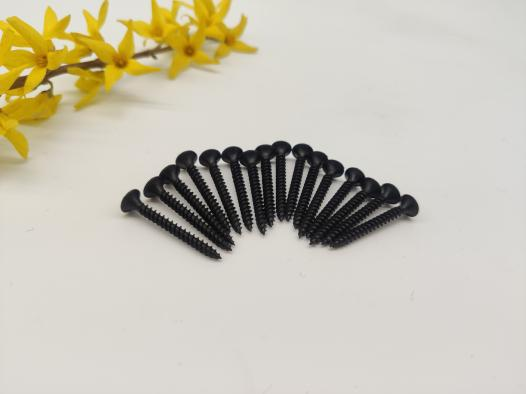
3, Hot dip galvanizing
Hot zinc dipping is to immerse the steel member after rust removal into the zinc solution melted at high temperature at about 600℃, so that the surface of the steel member is attached with a zinc layer. The thickness of the zinc layer shall not be less than 65μm for thin plate less than 5mm, and not less than 86μm for thick plate 5mm and above. Thus play the purpose of corrosion prevention.
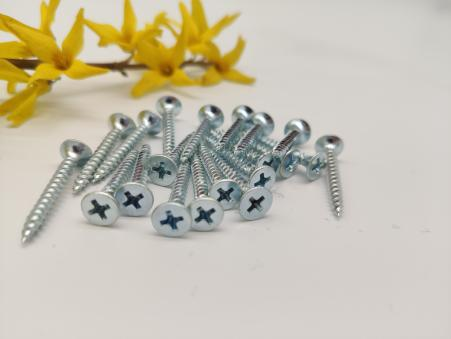
4, Dacroll
DACROMET is a DACROMET translation and abbreviation, DACROMET, DACROMET rust, Dicron. It is a new anticorrosive coating with zinc powder, aluminum powder, chromic acid and deionized water as the main components. There is no hydrogen embrittlement problem, and the torque-preload consistency is very good. If the environmental protection of hexavalent chromium is not considered, it is actually most suitable for high strength fasteners with high anticorrosion requirements.
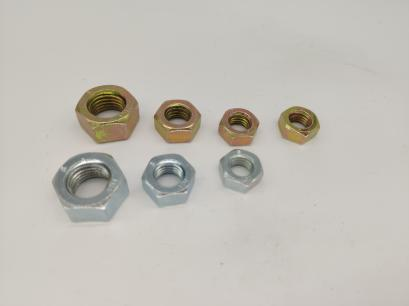
5, Electric galvanizing
Electrogalvanizing, also known as cold galvanizing in the industry, is the process of using electrolysis to form uniform, dense and well-combined metal or alloy deposition layer on the surface of the workpiece. Compared with other metals, zinc is relatively cheap and easy to coat a metal, a low value corrosion resistance electroplating, is widely used to protect steel parts, especially against atmospheric corrosion, and used for decoration. Plating techniques include slot plating (or hang plating), roll plating (suitable for small parts), blue plating, automatic plating and continuous plating (suitable for wire, strip).
Electrogalvanizing is the most commonly used coating for commercial fasteners. It is cheaper and better looking, and can come in black or army green. However, its anticorrosion performance is general, its anticorrosion performance is the lowest in zinc plating (coating) layer. General electrogalvanizing neutral salt spray test within 72 hours, there are also the use of special sealant, making the neutral salt spray test more than 200 hours, but the price is expensive, is 5~8 times the general galvanizing.
Fasteners for structural parts are generally colored zinc and white zinc, such as 8.8 commercial grade bolts.
6, Chrome plated
Chrome plating is mainly to improve the surface hardness, beauty, rust prevention. Chromium plating has good chemical stability and does not react in alkali, sulfide, nitric acid and most organic acids, but is soluble in hydrohalic acid (such as hydrochloric acid) and hot sulfuric acid. Chromium is superior to silver and nickel because it does not change color and retains its reflectivity for a long time when used.
7, Nickel plating
Nickel plating is mainly wear-resistant, anti-corrosion, anti-rust, generally thin thickness of the process is divided into electroplating and chemical two categories.
8, Zinc impregnation
The principle of powder zincizing technology is to place the zincizing agent and iron and steel parts in the zincizing furnace and heat to about 400 ℃, and the active zinc atoms will infiltrate into the iron and steel parts from the outside to the inside. At the same time, the iron atoms spread from the inside out, which forms a zinc-iron intermetallic compound, or zinc coating, on the surface of the steel parts.
Fasteners, despite their small size, perform a very important task
Fasteners, despite their small size, perform a very important task – connecting various structural elements, equipment and appliances.They are used in everyday life and industry, in maintenance and construction work.A wide variety of fasteners are available on the market.But in order not to make the wrong choice, you need to know the varieties of these products and their main features.
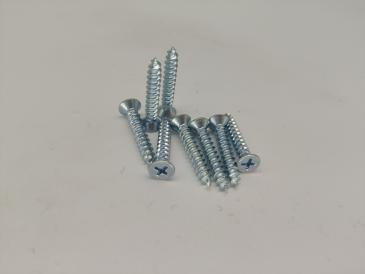
There are many ways to classify fasteners.One of them uses the existence of threads.With its help, you can create detachable connections, which are very popular in everyday life and industrial sites.Popular threaded fasteners include:Each element has a special purpose.For example, in Bulat-Metal you can see mounts for different tasks.Hex bolts are ideal for joining metal structures and equipment components, as well as self-tapping screws – for repair work involving wooden elements.The operating range of the stent determines its shape, size, material and other parameters.The screws on wood and metal are visually different – the former has a thinner thread and a deviation from the cap.
In the construction industry, structural bolts and nuts are widely used in the production of sheds, bridges, dams and power plants.In fact, the use of structural bolts and nuts is done alternately by welding metals, which means either structural bolts or arc welding using electrodes, depending on the need to join the steel plate and beam.Each connection method has its own advantages and disadvantages.
Structural screws used in building beam connections are made of high-grade steel, typically grade 10.9.Grade 10.9 means that the tensile strength density of the structural screw is about 1040 N/mm2, and it can withstand up to 90% of the total stress applied to the screw body in the elastic region without permanent deformation.Compared with 4.8 iron, 5.6 iron, 8.8 dry steel, structural screws have higher tensile strength and have more complicated heat treatment in production.
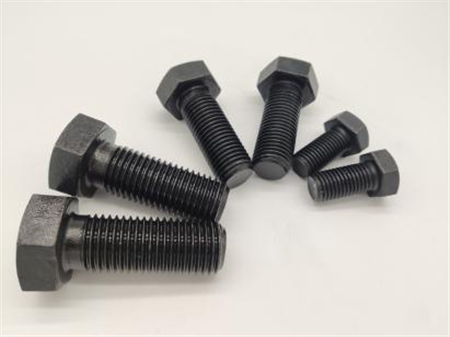
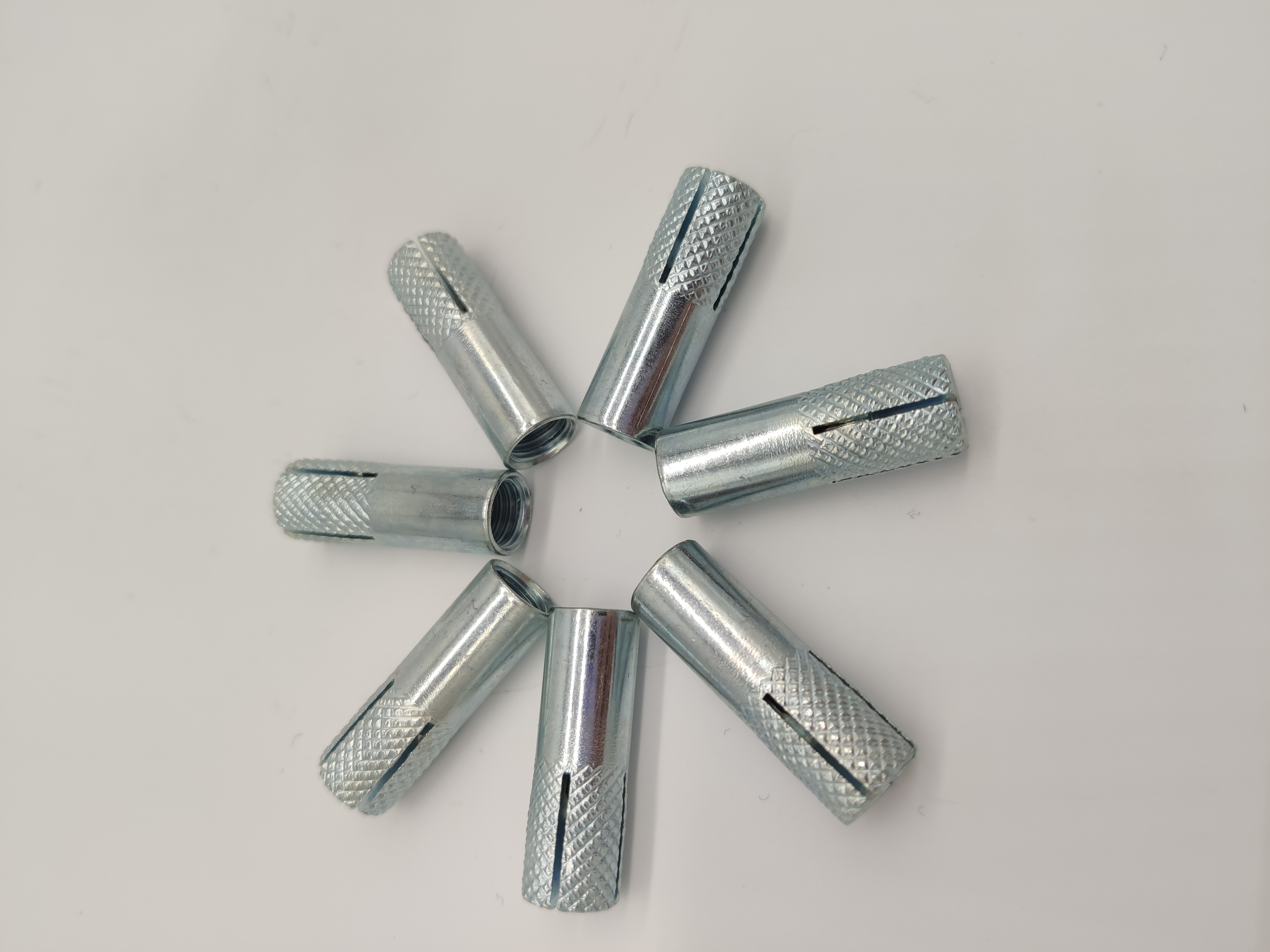
Post time: Aug-20-2022